Table of Contents
Binder Jetting
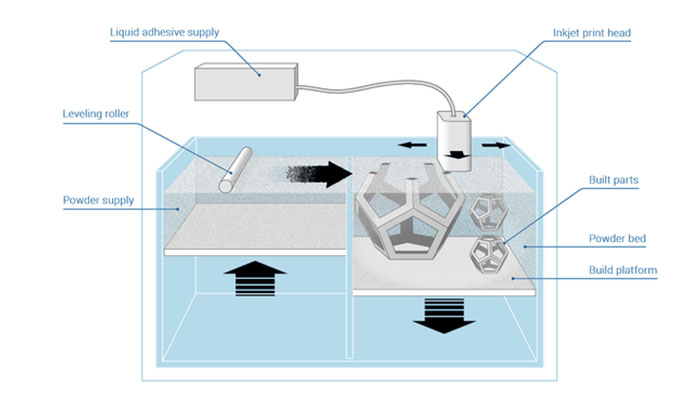
Understanding Binder Jetting Additive Manufacturing: A Comprehensive Guide
Binder Jetting is an innovative and versatile additive manufacturing (AM) method that stands out for its ability to create complex parts using a variety of materials. This blog provides an in-depth look at Binder Jetting, explaining how it works, its advantages and disadvantages, and its diverse applications. Let’s dive into the fascinating world of Binder Jetting and see how it is transforming manufacturing.
What is Binder Jetting?
Binder Jetting is an additive manufacturing process that involves the selective deposition of a binding agent onto a powder bed to create solid parts. This technology is known for its efficiency and ability to produce parts in a range of materials, including metals, ceramics, and polymers.
How Does Binder Jetting Work?
The Binder Jetting process involves several steps:
Design: The process begins with a digital 3D model, created using Computer-Aided Design (CAD) software. This model is then sliced into thin horizontal layers.
Powder Spreading: A layer of powdered material is spread across the build platform.
Binder Deposition: A print head moves across the powder bed, selectively depositing a liquid binding agent. The binder binds the powder particles together to form a solid layer.
Layering: The build platform lowers, and a new layer of powder is spread over the previous layer. The binder is again deposited to form the next layer. This process repeats layer by layer until the entire object is built.
Curing and Post-Processing: After printing, the part may need to be cured to strengthen the binding agent. Depending on the material and application, additional post-processing steps such as sintering, infiltration, or surface finishing may be required.
Advantages of Binder Jetting
Binder Jetting offers several benefits that make it a valuable manufacturing method:
Material Versatility: Binder Jetting can use a wide range of materials, including metals, ceramics, and polymers. This versatility allows for the creation of parts with diverse properties.
Complex Geometries: The process can produce intricate and complex geometries that would be difficult or impossible to achieve with traditional manufacturing methods.
Scalability: Binder Jetting is suitable for both small-scale and large-scale production, making it ideal for prototyping and mass production.
Cost-Effective: Binder Jetting generally has lower material costs and waste compared to other additive manufacturing methods. It also allows for the efficient use of expensive materials.
Speed: The Binder Jetting process can be faster than other 3D printing technologies, especially for large parts and high-volume production.
Disadvantages of Binder Jetting
While Binder Jetting has many advantages, it also has some limitations:
Mechanical Properties: The parts produced by Binder Jetting may have lower mechanical properties compared to those made with other methods like metal powder bed fusion. This can affect the strength and durability of the final product.
Post-Processing: Binder Jetting often requires extensive post-processing, such as curing, sintering, or infiltration, which can add time and cost to the production process.
Surface Finish: Parts made with Binder Jetting may have a rougher surface finish compared to those made with other additive manufacturing techniques. Additional finishing processes may be needed to achieve the desired surface quality.
Binder Limitations: The choice of binder can impact the final properties of the part, and some binders may not be suitable for certain applications or materials.
Applications of Binder Jetting
Binder Jetting’s versatility and efficiency make it suitable for a wide range of applications:
Prototyping: Binder Jetting is excellent for rapid prototyping, allowing designers to quickly create and test complex parts.
Aerospace: The technology is used to produce lightweight, complex components for aerospace applications, reducing material waste and cost.
Automotive: Binder Jetting is used to create intricate parts and prototypes for the automotive industry, enabling faster design iterations and testing.
Medical: The process is used to create custom implants, dental devices, and medical models with high precision.
Consumer Goods: Binder Jetting can produce detailed and customized consumer products, from jewelry to household items.
Conclusion
Binder Jetting is a powerful and versatile additive manufacturing method that offers numerous benefits, including material versatility, the ability to create complex geometries, and cost-effective production. While it has some limitations in terms of mechanical properties and post-processing requirements, ongoing advancements in Binder Jetting technology continue to expand its capabilities and applications.